1.1. Adquisición de habilidades en la asignación de condiciones de corte, elección de herramienta de corte y cálculo del tiempo principal.
2.1. Anote los datos de las condiciones de procesamiento para su variante;
2.2. Elección de la herramienta de corte, cálculo de las condiciones de corte;
2.3. registro de obra
3. Lista de accesorios
3.1. Papel de escribir, formato A4 - 4 hojas;
3.2. Una calculadora que realiza las funciones y x.
3.3 Programa de aplicación KOMPAS 3D V11
4. Información general
4.1. La perforación es uno de los métodos más comunes para hacer agujeros. La herramienta de corte aquí es un taladro, que permite obtener agujeros en un material sólido y aumentar el diámetro antes ...
agujero perforado El movimiento principal durante la perforación es de rotación, el movimiento de avance es de traslación.
Según la forma y el diseño, existen brocas helicoidales, con ranuras rectas, brocas de pluma, para taladrado profundo, anulares, de centrado, con ranuras para suministro de refrigerante, con placas multifacéticas. Las brocas están hechas con vástagos cilíndricos y cónicos.
Las principales dimensiones y ángulos de la hoja de perforación están estandarizados. La parte de corte del taladro está fabricada en acero R18, R6M5 y aleaciones duras.
Los vástagos de los taladros con vástago cónico tienen un cono Morse, fabricado de acuerdo con GOST 25557-82.
5. Orden de trabajo
5.1. Anote los datos de su opción (ver tabla 14);
5.2. Seleccione un taladro y establezca el valor de sus elementos geométricos.
5.3. Establezca la profundidad de corte t=D /2 (mm) al taladrar en metal sólido
t = , mm al perforar un agujero previamente hecho
5.4. Asigne una presentación. Al perforar agujeros sin factores limitantes, seleccionamos la fuerza de perforación máxima permitida. Al taladrar agujeros, el avance recomendado para taladrar se puede aumentar hasta 2 veces.
Entonces, mm / rev: al perforar acero, hierro fundido, cobre y aleaciones de aluminio
5.5. Asignar la velocidad del movimiento de corte principal
V = , m/min - al perforar
V = , m/min - al escariar
Km - coeficiente para el material procesado
-factor de corrección teniendo en cuenta la profundidad del agujero que se está procesando.
5.6. Determinar la velocidad del husillo
rpm
D- diámetro del agujero, mm.
Corregimos la velocidad del husillo de acuerdo con los datos de pasaporte de la máquina. Aceptamos el valor más pequeño más cercano norte rpm
5.7. Determinar la velocidad de corte real , m/min
5.8. Determinar el par
Mcr = 10 cm Kp - al escariar
Valores de coeficientes y exponentes
5.9. Determinar la potencia gastada en el corte.
(eficiencia)
5.10. Determinar el tiempo principal
5.11. Conclusión: la potencia de la máquina le permite realizar el procesamiento en este modo de corte. En el caso de que N res.rev > N w - es necesario determinar la carga de la máquina en términos de potencia
Para cortes de corta duración (hasta 1 min), se permite sobrecargar el motor eléctrico de la máquina en un 25% de su potencia nominal. En caso de sobrecarga mayor, reduzca la velocidad o tome una máquina más potente.
6. Requisitos para el registro del cálculo
6.1. La tarea completa se redacta en hojas estándar de formato A4. La primera página es la página de título (ver Apéndice 1)
Ejemplo de finalización de tareas
Opción número 31
Tarea: En una máquina de perforación vertical 2H 135, se perfora un agujero con un diámetro D y una profundidad l. Es necesario: seleccionar una herramienta de corte, asignar un modo de corte, determinar el tiempo principal (ver diapositiva 1, Apéndice 3.1).
Tabla 13
Elección de la herramienta de corte(ver diapositiva 2 apéndice 3.2)
Broca Ø18 con vástago cónico de acero P18. GOST 10903-64
Elementos geométricos: forma de afilado - doble con una punta en el borde transversal.
Ángulos de perforación 2 φ = 118°, 2 φ1 = 70 0 .
ﮯγ = 25°
Asignación de elementos de corte.(ver diapositiva 3 apéndice 3.3)
1. Determinar la profundidad de corte
t = 18/2 = 9 mm
2. Asignar el saque
Entonces \u003d (0.33 - 0.38) mm / rev
K 1 = 0,9 (profundidad de taladrado hasta 5D)
Entonces So \u003d (0.33 - 0.38) * 0.9 \u003d (0.3 - 0.34) mm / rev
Corregimos según el pasaporte de la máquina.
Entonces = 0,28 mm/rev
3. Determinar la velocidad de corte
V = , m/min
Сv = 9,8 q = 0,4 y= 0,5 m = 0,2
- factor de corrección general para la velocidad de corte
Km = Kr Kr = 0,95 n=1 Km = 0,9
-factor de corrección teniendo en cuenta la influencia del material de la herramienta
-factor de corrección teniendo en cuenta la profundidad del agujero que se está procesando.
0,9 1 0,85 = 0,765
V = 0,765 = 21 m/min
4. Velocidad del husillo
n d \u003d 355 rpm (según el pasaporte de la máquina)
5. Determinar la velocidad de corte real
6. Determinar el par
Mcr = 10 cm Kp - al perforar
cm = 0,0345 q = 2 y = 0,8
Kp \u003d Kmr \u003d 0.9
Mcr \u003d 0.0345 0.9 \u003d 3.62 N·m
7. Determinar la potencia gastada en el corte
N = = 0,13 kW
Comprobar si la potencia de accionamiento de la máquina es suficiente
(eficiencia)
Nshp = 4,5 0,8 = 3,6 kW
8. Determinar el tiempo principal
y=7 mm.
(Ver diapositiva 4 Apéndice 3.4)
Croquis de procesamiento (ver diapositiva 5 Apéndice 3.5)
Tarea: Se perfora un agujero con un diámetro D y una profundidad l en una máquina de perforación vertical 2H135.
Es necesario: seleccionar una herramienta de corte, asignar elementos de modo de corte; determinar el tiempo principal.
Tabla 14
número de opción | Material de la pieza | D | yo | Agujero | Tratamiento |
milímetro | |||||
Acero 10 σv \u003d 35 kgf / mm 2 | 15H12 | Sordo | Enfriado | ||
Acero 40 σv = 45 kgf/mm2 | 22H14 | mediante | Enfriado | ||
Hierro fundido gris 200HB | 16Н14 | mediante | sin refrigeración | ||
Acero 40 X σv = 55 kgf / mm 2 | 18Н13 | mediante | Enfriado | ||
Acero 20 X 170 HB | 20Н14 | mediante | Enfriado | ||
Hierro fundido gris 210 HB | 10Н14 | Sordo | sin refrigeración | ||
Acero 12X3 σv = 45 kgf/mm2 | 19.2H14 | Sordo | Enfriado | ||
Acero 35 X σv \u003d 48 kgf / mm 2 | 24Н14 | Sordo | Enfriado | ||
Hierro fundido gris 170 HB | 18,25 | mediante | sin refrigeración | ||
Acero 20 σv \u003d 38 kgf / mm 2 | 15H12 | Sordo | Enfriado | ||
Acero 45 σv \u003d 44 kgf / mm 2 | 26Н12 | Sordo | Enfriado | ||
Hierro dúctil 180 HB | 24Н12 | Sordo | sin refrigeración | ||
Acero 5 X NM σv \u003d 70 kgf / mm 2 | 18Н12 | mediante | Enfriado | ||
Acero U7A σv \u003d 58 kgf / mm 2 | 20Н12 | mediante | Enfriado | ||
Acero 65G σv \u003d 50 kgf / mm 2 | 25H12 | mediante | Enfriado | ||
Hierro fundido gris 210HB | 28Н12 | Sordo | sin refrigeración | ||
Acero 40 X 13 σv = 65 kgf/mm2 | 24Н12 | Sordo | Enfriado | ||
Acero 9 x C σv \u003d 60 kgf / mm 2 | 20Н12 | mediante | Enfriado | ||
Hierro dúctil 220 HB | 26Н12 | mediante | sin refrigeración | ||
Acero 40 X C 225 HB | 8Н12 | mediante | Enfriado | ||
Acero 30L σv=50 kgf/mm | 6Н12 | mediante | Enfriado | ||
Acero A20 σv \u003d 30 kgf / mm 2 | 12H12 | mediante | Enfriado | ||
Acero 35 σv = 50 kgf/mm2 | 14H12 | Sordo | Enfriado | ||
Hierro fundido gris 175 HB | 16Н12 | Sordo | sin refrigeración | ||
Acero 40 G σv = 55 kgf/mm2 | 16.8H12 | Sordo | Enfriado | ||
26 | Acero X12M δv = 60 kgf/mm2 | 17.2H12 | mediante | Enfriado | |
Acero HVG σv = 55 kgf/mm | 18.25H12 | mediante | Enfriado | ||
Hierro fundido gris 170 HB | 24Н12 | mediante | sin refrigeración | ||
Latón LMtsZh 52-4-1 100 HB | ZONA12 | mediante | sin refrigeración | ||
Bronce BRAZO 11-6-6 200 HB | 24Н12 | mediante | sin refrigeración |
El taladrado se realiza con diferentes herramientas de corte, según el tipo de pieza, la precisión requerida y el acabado superficial deseado.
Hay espacios en blanco con orificios preparados por fundición, forja o estampado, y espacios en blanco sin orificios preparados previamente.
El mecanizado de agujeros en piezas de trabajo que no tienen agujeros preparados siempre comienza con la perforación.
1. Ejercicios
La perforación de agujeros poco profundos se realiza con un bolígrafo y brocas helicoidales.
Taladro de plumas. El primer taladro se muestra en la fig. 159. La parte cortante del taladro es una cuchilla plana 3, que pasa a la varilla 4. Dos bordes cortantes 1 y 2 del taladro están inclinados entre sí, generalmente en un ángulo de 116-118 °, pero este ángulo puede ser igual a de 90 a 140 °, dependiendo de la dureza del material de la pieza: cuanto más duro es el material, mayor es el ángulo.
Los taladros de pala son ineficientes, además, al perforar, se alejan del eje del orificio. A pesar de ello, en ocasiones se utilizan para trabajos no críticos, debido a la sencillez del diseño de este tipo de taladros y su bajo coste.
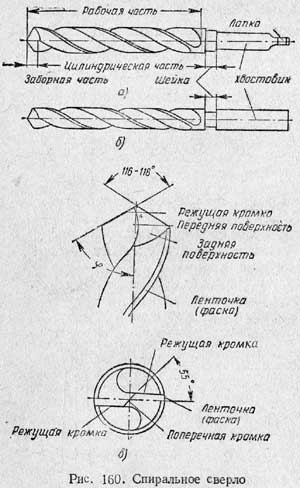
Brocas helicoidales. Actualmente, la perforación se realiza principalmente con brocas helicoidales. En la fig. 160 muestra tal ejercicio. Consiste en parte de trabajo y caña(cónico según la Fig. 160, a o cilíndrico según la Fig. 160, b) para fijar el taladro en el orificio cónico de la caña del contrapunto o en el mandril.
El vástago cónico tiene pata, que sirve como tope al golpear el taladro (Fig. 160, a).
La parte de trabajo del taladro helicoidal es un cilindro con dos ranuras en espiral (o mejor dicho, helicoidales) que sirven para formar los bordes cortantes del taladro y sacar las virutas. La parte delantera del taladro (Fig. 160, c) está afilada a lo largo de dos superficies cónicas y tiene cara delantera, cara trasera, dos filos de corte, conectado puente(borde transversal). dos estrechos cintas(chaflanes), que discurren a lo largo de las ranuras helicoidales de la broca, sirven para la correcta dirección y centrado de la broca.
El ángulo de la punta de la broca 2φ suele ser de 116 a 118°. Para taladrar en materiales duros, este ángulo se aumenta a 140°, y para taladrar en materiales blandos, se reduce a 90°.
Los taladros están hechos de acero de aleación 9XC, acero de alta velocidad P9 y P18, y también de acero de aleación con placas de aleación dura soldadas.
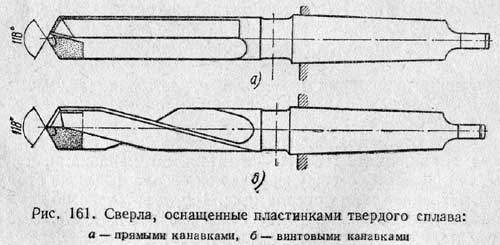
Las brocas equipadas con insertos de carburo se muestran en la fig. 161. Los taladros con ranuras rectas (Fig. 161, a) son más fáciles de fabricar, pero les resulta difícil sacar las virutas del orificio; por lo general, se utilizan para perforar hierro fundido y otros metales frágiles, cuando la profundidad del orificio no supera los dos o tres diámetros. Los taladros con ranuras helicoidales (Fig. 161, b) eliminan las virutas del orificio con mayor facilidad, por lo que se recomienda su uso al perforar materiales viscosos.
2. Afilado de brocas helicoidales
El afilado de las brocas helicoidales se realiza en rectificadoras especiales. Sin embargo, el tornero a veces tiene que afilar las brocas a mano con un afilador convencional.
Al afilar brocas, se deben observar las siguientes condiciones:
1. Los bordes cortantes del taladro deben estar simétrico, es decir, situados en ciertos e iguales ángulos con el eje del taladro y tienen la misma longitud.
2. El borde transversal (puente) debe ubicarse en un ángulo de 55 ° con respecto a los bordes de corte (Fig. 160, c.).
Un taladro afilado de esta manera funcionará bien.
En la fig. 162 muestra los agujeros obtenidos al perforar con brocas correctamente e incorrectamente afiladas. Con la misma longitud de los filos (Fig. 162, a), el diámetro del orificio perforado es igual al diámetro del taladro. Si un borde es más largo que el otro (Fig. 162, b), entonces el diámetro del orificio es mayor que el diámetro del taladro. Esto puede conducir al matrimonio y desactivar rápidamente el taladro debido a la carga desigual de los filos.
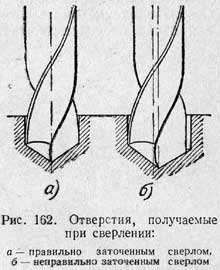
La corrección del afilado del taladro se verifica mediante una plantilla combinada especial con tres recortes (Fig. 163, a); uno de los cortes verifica el ángulo en la parte superior del taladro y la longitud de los bordes cortantes (Fig. 163, b), el segundo corte: el ángulo de afilado del borde cortante en el diámetro exterior del taladro (Fig. 163, c), el tercero: el ángulo entre el puente y el filo (Fig. 163, d).
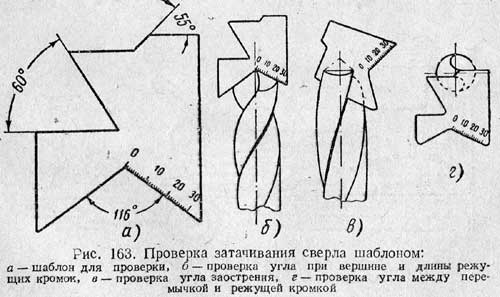
3. Taladros de fijación
El método de fijación del taladro depende de la forma de su vástago. Taladro con vástago cilíndrico fijado en la caña del contrapunto por medio de cartuchos especiales (Fig. 164); ejercicios con vástago cónico se fijan directamente en el orificio cónico de la caña del contrapunto (Fig. 165). Los mangos cónicos de las herramientas, así como los orificios cónicos de los husillos y las púas de los tornos, se fabrican de acuerdo con el sistema Morse. Los conos Morse están numerados 0, 1, 2, 3, 4, 5, 6; Cada número corresponde a un tamaño determinado. Si el cono del taladro es más pequeño que el orificio cónico de la caña del contrapunto, coloque el vástago 1 del taladro manguito adaptador 2 (Fig. 166) y luego el manguito, junto con el taladro, se inserta en el orificio de la caña del contrapunto de la máquina.
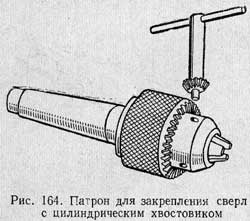
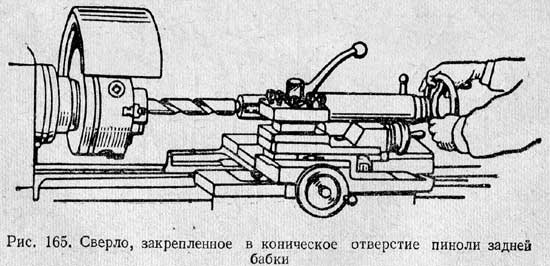
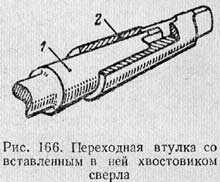
Antes de insertar la broca en la caña del contrapunto, es necesario limpiar a fondo el vástago de la broca, así como el orificio de la caña, de la suciedad.
Para retirar el taladro de la caña del contrapunto, gire el volante hasta que la caña se introduzca en la carcasa del contrapunto hasta su posición final. En esta posición, el tornillo descansará contra el extremo del vástago y lo empujará hacia afuera.
4. Técnicas de perforación
Preparación para la perforación. Al perforar un orificio con una longitud de más de dos diámetros de broca, se recomienda que primero se fije rígidamente el orificio en la caña con uno corto. Luego, la broca posterior se guiará mejor y se desplazará menos hacia un lado.
Avance de perforación. El taladro se alimenta girando el volante del contrapunto (Fig. 165).
Al perforar un agujero profundo broca helicoidal es necesario de vez en cuando retirar el taladro del agujero en movimiento de la máquina y sacarlo de las virutas; esto evita la rotura del taladro. También es necesario asegurarse de que al perforar con brocas normales, la profundidad del orificio no sea mayor que la longitud de la ranura helicoidal de la broca, de lo contrario, las virutas no podrán salir de las ranuras y la broca se romperá.
Perforación de agujeros ciegos. Para taladrar agujeros de una determinada longitud, es conveniente utilizar los riesgos de las púas del contrapunto (ver Fig. 165). Girando ma-empuje el taladro hasta que penetre profundamente en el material con toda la parte de entrada, y al mismo tiempo observe el riesgo correspondiente en las púas. Luego, al girar el volante del contrapunto, la canilla se mueve hasta que sale del cuerpo por el número deseado de divisiones.
Cuando no hay divisiones en las púas, se puede aplicar el siguiente método. Marque la longitud requerida del orificio en el taladro con tiza y mueva la pluma hasta que el taladro penetre profundamente en las marcas.
A veces, al perforar, se escucha un chirrido metálico característico. Esta es una señal de un orificio desalineado o de un taladro desafilado. En tales casos, debe detener inmediatamente la alimentación, detener la máquina, averiguar y eliminar la causa del chirrido.
Antes de detener la máquina durante la perforación, debe retirar el taladro del orificio. Es imposible parar la máquina mientras la broca está en el agujero, esto puede provocar el atascamiento de la broca y su rotura.
5. Condiciones de corte para taladrado y escariado
Velocidad de corte de perforación El acero al carbono de dureza media, el hierro fundido gris y el bronce con brocas de acero de alta velocidad se pueden tomar igual a 20-40 m / min.
El taladro se alimenta en un torno a mano, moviendo lentamente la caña del contrapunto, como se muestra en la fig. 165. Un avance excesivo y desigual puede provocar la rotura de la broca, especialmente cuando se utilizan brocas de diámetro pequeño.
A veces, al taladrar, también se usa avance mecánico (ver Fig. 167). En este caso, el taladro se fortalece con la ayuda de juntas especiales o un casquillo en el portaherramientas. Al taladrar con avance mecánico, la velocidad de avance se toma igual a: para brocas con un diámetro de 6 a 30 mm para acero al carbono de dureza media - de 0,1 a 0,35 mm1rev; para hierro fundido - de 0,15 a 0,40 mm / rev.
Al escariar, el borde transversal de la broca no participa en el trabajo. Debido a esto, la fuerza de avance se reduce significativamente y también se reduce la retirada del taladro; esto le permite aumentar la cantidad de avance aproximadamente 1½ veces en comparación con el avance de una broca del mismo diámetro al perforar material sólido.
Velocidad de corte de escariado puedes tomar lo mismo que al perforar.
Se recomienda perforar y escariar acero y aluminio con enfriamiento de emulsión en una cantidad de al menos 6 l / min; el hierro fundido, el latón y el bronce se taladran y escarian sin refrigeración. Sin embargo, debe tenerse en cuenta que debido a la disposición horizontal de los agujeros que se están maquinando, el refrigerante apenas llega al lugar donde se forman las virutas. Por lo tanto, para perforaciones profundas en materiales difíciles de mecanizar, se utilizan brocas con canales internos, a través de los cuales se suministra refrigerante a alta presión a los filos de corte.
6. Métodos de trabajo de alto rendimiento para taladrado y escariado
Sustitución de alimentación manual mecánica. Los innovadores en la producción, para mecanizar el suministro de un taladro, utilizan dispositivos sencillos y económicos que facilitan la mano de obra y ahorran tiempo. Uno de estos dispositivos se muestra en la Fig. 167.
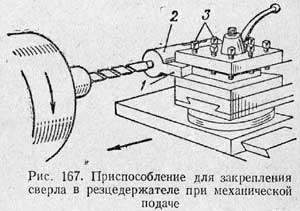
El dispositivo es un soporte de acero 2 con una teja 1, fijado con pernos 3 en el portaherramientas. El soporte tiene un orificio cónico para fijar el vástago de la broca y un orificio para sacar la broca. El plano inferior de la teja 1 está cepillado o fresado de manera que cuando se fija en el portaherramientas, la broca queda exactamente (sin distanciadores) colocada a la altura de los centros. Para instalar el taladro a lo largo del eje del orificio en un plano horizontal, se marca un riesgo en la corredera inferior de la pinza. Tal dispositivo es muy efectivo en la fabricación un número grande piezas con agujeros, ya que en este caso la perforación se realiza con un avance mecánico del taladro desde la pinza; usarlo reduce el tiempo de procesamiento y facilita el trabajo del tornero.
Para mecanizar el avance de la broca al perforar agujeros diametro largo en las condiciones de producción única y a pequeña escala, el innovador tornero camarada Buchnev hizo un dispositivo (Fig. 168, a), que permite mover el contrapunto con poco esfuerzo. Este dispositivo es el siguiente. Un soporte angular 5 está atornillado a la placa del contrapunto, en el que se colocan los rodillos 1 y 2. La rueda dentada de accionamiento 7 y el mango 6 se sientan en el rodillo 1. En el rodillo 2 hay una rueda dentada 3 y una rueda 4, que encaja con la barandilla de la cama. La rotación del mango 6 a través de las ruedas 7 y 3 se transmite a la rueda 4, que rueda a lo largo del riel de la máquina y mueve el contrapunto a lo largo del bastidor.
El torno de corte de tornillos 1K62 de la planta Krasny Proletarian prevé el reemplazo del avance manual del taladro (broca, escariador) por uno mecánico. Para hacer esto, la pinza tiene un bloqueo especial (Fig. 168, b), que está incluido en la marea del contrapunto. Usando un dispositivo tan simple, puede conectar el carro de la pinza a la placa del contrapunto y, al soltar la placa del contrapunto del marco, activar la alimentación mecánica más ventajosa de la pinza.
Al mismo tiempo, la productividad laboral aumenta significativamente. Además de esta ventaja, este método de avance permite taladrar (perforar, escariar) agujeros a la profundidad requerida, contando a lo largo del dial de avance longitudinal o utilizando un tope longitudinal (limitador de longitud).
Uso de taladros con afilado especial.. Para aumentar la productividad de la mano de obra, los innovadores de producción utilizan el rectificado de puentes, el afilado doble de brocas y las brocas sin puente.
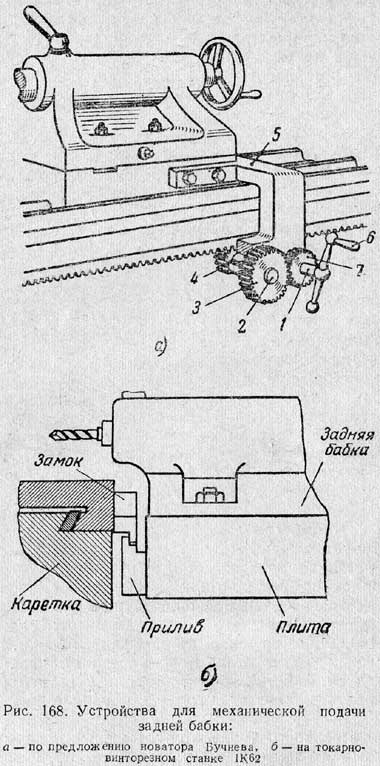
Taladro de tierra doble mostrado en la fig. 169, a. Su parte de admisión tiene bordes cortantes rotos: inicialmente cortos en un ángulo de 70-75° y alargados hacia la parte superior, en un ángulo de 116-118°. Dichos taladros se desgastan menos de lo normal y se caracterizan por una mayor durabilidad: 2-3 veces más cuando se taladra acero y 3-5 veces más cuando se taladra hierro fundido.
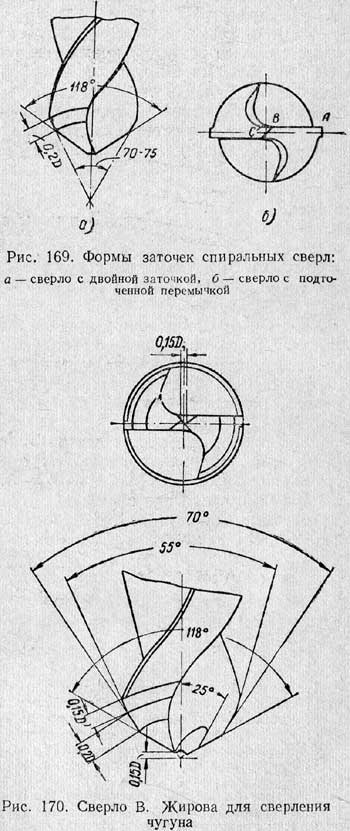
Para reducir la fuerza de avance durante la perforación, es útil socavar el puente en la sección BC (Fig. 169, b). Con una socavación de este tipo, no solo disminuye el borde transversal, sino que también aumenta el ángulo de inclinación, lo que facilita las condiciones de corte.
En la fig. 170 muestra una broca de alto rendimiento fabricada con acero de alta velocidad por un perforador de alta velocidad de la planta de máquinas-herramienta del Volga Medio V. Zhirov. El taladro está destinado al taladrado de hierro fundido.
El taladro Zhirov, a diferencia del taladro que se muestra en la Fig. 169, a, está hecho con un triple cono en la parte superior, con una superficie frontal afilada y un puente cortado. La presencia de un rebaje en lugar de un puente facilita en gran medida la penetración del taladro en el metal que se está procesando, por lo que la fuerza axial se reduce de 3 a 4 veces al perforar hierro fundido. Esto le permite aumentar la velocidad de avance de la broca y reducir el tiempo de la máquina al menos a la mitad.
Para aumentar la durabilidad, la parte de admisión del taladro Zhirov tiene tres filos de corte rotos, inicialmente cortos, formando un ángulo de 55 °, luego más largos, con un ángulo de 70 ° y, finalmente, los más largos, con un ángulo en la parte superior. de 118°.
La presencia de filos de corte cortos con un ángulo de 55° contribuye a aumentar significativamente la vida útil de la broca (cuando se trabaja con avances elevados) en comparación con los diseños de brocas convencionales.
7. Matrimonio durante la perforación y medidas para prevenirlo
El tipo principal de matrimonio durante la perforación es la eliminación del taladro de la dirección requerida, que se observa con mayor frecuencia al perforar agujeros largos.
La retracción del taladro ocurre: cuando se perforan piezas de trabajo cuyas superficies finales no son perpendiculares al eje; cuando se trabaja con taladros largos; cuando se trabaja con brocas mal afiladas, en las que un filo es más largo que el otro; al perforar metal que tiene hoyos o contiene sólidos.
La deriva de la broca cuando se trabaja con brocas largas se puede reducir perforando previamente el orificio con una broca corta del mismo diámetro.
Si en el camino del taladro en el material de la pieza hay conchas o inclusiones sólidas, en este caso es casi imposible evitar que el taladro se deslice. Sólo puede reducirse reduciendo el avance, lo que a su vez será un medio para evitar posibles roturas de la broca.
preguntas de examen 1. ¿Qué tipos de taladros se utilizan para taladrar en tornos?
2. Nombre los elementos de un taladro helicoidal.
3. Cuéntenos sobre las reglas para afilar brocas.
4. ¿Cómo afectará el afilado incorrecto del taladro al tamaño del agujero?
5. ¿Cómo se fijan los taladros en la máquina?
6. Cuéntenos sobre los métodos de perforación a través de agujeros, agujeros ciegos:
7. ¿Qué tipo de refrigeración se utiliza para perforar?
8. Cuéntenos sobre los métodos de perforación avanzados.
9. ¿Cómo evitar el deslizamiento de la broca?
Fuerzas de corte, par y potencia de perforación
Durante el proceso de corte, el taladro experimenta resistencia por parte del material que se está procesando. En cada punto del filo de corte actúan fuerzas de resistencia. Reemplacémoslos con la fuerza resultante aplicada al punto A a una distancia aproximadamente igual a D /4 del eje de perforación. Este último se puede descomponer en tres componentes de fuerza. R x , ru y Pz (fig. 72.)
Arroz. 72. Fuerzas que actúan sobre un taladro
fuerza de resistencia R x dirigida a lo largo del eje del taladro. Fuerza que actúa en la misma dirección. R pag en el borde transversal, fuerza de fricción Rt cintas en la superficie del agujero, las fuerzas de resistencia que actúan sobre el taladro a lo largo de su eje, sobre el eje X reemplazar la fuerza resultante PAG0 , que se denomina fuerza axial o fuerza de avance. Es superado por el mecanismo de alimentación de la máquina. Este último debe transferir la fuerza axial al husillo de la máquina. R" 0 capaz de vencer la fuerza PAG0 . La fuerza axial máxima permitida por el mecanismo de avance de la máquina se indica en su pasaporte.
Fórmulas para calcular la fuerza axial y el momento al perforar:
Definición de fuerza PAG0 y momento mcr producido de acuerdo con fórmulas empíricas obtenidas experimentalmente. Para brocas de acero para herramientas al mecanizar piezas de acero y hierro fundido, tienen la siguiente forma:
; , kgf mm - al perforar;
; , kgf mm al escariar.
dónde: C pag y Cm - coeficientes que dependen del metal que se está procesando, la forma de las condiciones de afilado y corte del taladro;
zp, XP , sí , z M , x M y yM - el grado de influencia del diámetro de la broca D , profundidad del corte t , archivo s para fuerza axial P0 y par de perforación METRO ;
Kp y kilómetros – factores de corrección para condiciones de perforación modificadas;
Fuerzas radiales ru , multidireccionales, son balanceadas (S ru = 0). Fuerza Pz crea un momento de resistencia al corte METRO en los filos de corte principales, y la fuerza R t', tangente a la cinta, es el momento de fricción sobre ella (generalmente se desprecia).
La influencia relativa de los elementos de perforación en la fuerza de corte y el par durante la perforación se muestran en la Tabla 16.
Tabla 16. Influencia de los elementos de perforación en la fuerza axial P0 y par METRO
Momento de resistencia al corte corte M superado por el mecanismo del movimiento principal, es decir, el par en el husillo de la máquina mcr . En cada paso del husillo de la máquina, la potencia norte constante, momento mcr variable. Depende de la velocidad (velocidad) PAGS en esta etapa se determina:
mcr= 716200 1,36 () kgf mm; norte = N dv · h , kilovatios,
mcr= 974000() kgf mm.
Conociendo el momento de resistencia METRO , podemos determinar la potencia efectiva N e gastado en cortar durante la perforación,
La potencia de avance del taladro es aproximadamente el 1% de la potencia y no se tiene en cuenta en los cálculos. La potencia determina la potencia que debe tener el motor eléctrico de la máquina para asegurar un determinado proceso de corte:
, kilovatios
La máquina es adecuada para las condiciones de perforación dadas si N w > N e .
6.4. La influencia de varios factores en la fuerza axial y el momento durante la perforación. Para fuerza axial PAG0 y momento de resistencia de corte METRO las propiedades del material que se está procesando, los parámetros geométricos de la broca, los elementos del corte (diámetro, avance), etc.
6.4.1. Propiedades del material procesado. Cuanto mayor sea la resistencia a la tracción σ en y dureza media pensión material, cuanto mayor sea su resistencia al corte, mayores serán los valores PAG0 y METRO . Para brocas de acero rápido se obtuvieron experimentalmente las siguientes dependencias:
, y - para acero;
, y - para hierro fundido.
dónde: C pag y Cm son coeficientes que dependen de las condiciones de corte.
6.4.2. Parámetros geométricos del taladro.. Con ángulo creciente w fuerza axial PAG0 y momento METRO disminución debido al aumento de los ángulos frontales x en los filos de corte principales y facilitar la evacuación de la viruta. Esquina j , (2j ) afecta los componentes de la fuerza de corte y el momento por analogía con el torneado: con una disminución en el ángulo, la fuerza axial PAG0 disminuye y la tangencial Pz aumenta, por lo que aumenta METRO . Con ángulo decreciente 2 j resistencia al corte debido al aumento x disminuye, pero al mismo tiempo aumenta el ancho del corte y disminuye su espesor. Esto último conduce a un aumento de la deformación (las virutas delgadas se deforman más completamente) y, en consecuencia, a un aumento de la fuerza. R x y momento METRO . Ángulo de inclinación del borde transversal d > 90° (ver fig. 72) y esto aumenta significativamente la fuerza axial PAG0 . Anteriormente se señaló que la fuerza que actúa sobre el borde transversal Rp = 0,55PAG0 . Para reducirlo, la longitud del borde se reduce afilando, su ángulo de ataque aumenta, creando así condiciones de corte más favorables cerca de él. por la cantidad METRO la geometría del borde transversal tiene poco efecto. El afilado doble del taladro también tiene poco efecto en PAG0 y METRO .
Diámetro y avance de la broca. Al aumentar el diámetro de la broca D y presentación s el ancho y el espesor de la capa cortada aumentan, por lo tanto, aumentan las fuerzas y los momentos de corte. Se ha establecido experimentalmente que el diámetro de la broca afecta PAG0 en mayor medida (1) que el tono (0,8). Para explicarlo, podemos trazar una analogía con el torneado, donde la profundidad de corte t afecta las fuerzas de corte en mayor medida que el avance (ver), y al taladrar t = D /2 mm. El avance incide aproximadamente en el mismo grado (0,8) sobre la fuerza axial PAG0 y par METRO , y el diámetro incide en mayor medida (1.9) sobre METRO y en un grado menor PAG0 (una). Esto se debe al hecho de que a medida que aumenta el diámetro, aumenta la fuerza. Pz , creando un momento METRO , y al mismo tiempo aumenta la longitud del brazo sobre el que actúa esta fuerza, lo que también contribuye a un aumento de METRO (arroz.).
Refrigerante. El aporte de refrigerante a la zona de corte facilita el arranque de viruta, reduce el trabajo de fricción y ralentiza el desgaste de la broca. Contribuye a la reducción de la fuerza axial. PAG0 y momento METRO hasta un 25 % cuando se procesan piezas de acero y hasta un 15 % cuando se procesa hierro fundido.
Desgaste del taladro
La naturaleza y la naturaleza del desgaste de los taladros y cortadores son los mismos. Cuando se procesan materiales viscosos (aceros, etc.), los taladros de alta velocidad desgastan las superficies delantera y trasera del taladro (Fig. 73), y para los taladros de carburo, las superficies frontales se desgastan ligeramente.
Arroz. 73. La naturaleza del desgaste del taladro: PERO- en la superficie posterior; B- por cinta; A- en las esquinas; GRAMO- en el frente
Cuando se procesan materiales quebradizos (hierro fundido, plásticos, etc.), las superficies traseras y las esquinas del taladro se desgastan principalmente. Las superficies delantera y trasera de la broca se desgastan más intensamente en la periferia, ya que aquí la velocidad de corte es máxima y las esquinas de la broca, al ser un punto débil, están muy calientes y destruidas. El patrón de desgaste de las brocas es aproximadamente el mismo que el de las fresas durante el torneado (Fig. 74).
Arroz. 74. La naturaleza del curso de desgaste del taladro desde el momento del trabajo.
Se recomienda una evaluación del desgaste: cuando se mecanizan materiales viscosos, a lo largo de la longitud de desgaste a lo largo de las superficies posteriores h , para materiales frágiles - a lo largo de la longitud de desgaste de las esquinas hola Valor de desgaste admisible - criterio de desgaste al taladrar con taladros de alta velocidad:
h Z cr= 0,4 ... 1,2 mm, al procesar acero;
Cuando se mecaniza hierro fundido con brocas de alta velocidad, se toma como criterio de desgaste el desgaste a lo largo de las esquinas.
h\u003d 0,4 ... 1,2 mm - procesamiento con un taladro de acero de alta velocidad;
h= 0,9 ... 1,4 mm. – mecanizado con broca de aleación dura;
Período de durabilidad T , min, depende del diámetro de la broca y del material que se esté procesando.
T= (1,0…1,25)∙D – procesamiento de acero con taladros de alta velocidad;
T= (1,25…1,5) D – procesamiento de hierro fundido con taladros de alta velocidad;
T= (1,5…2,0) D – mecanizado de hierro fundido con brocas de carburo.
Como resultado de los experimentos realizados al perforar acero con taladros de alta velocidad, se obtuvo la siguiente dependencia:
De los resultados obtenidos se puede observar que el desgaste de la broca se ve más afectado por la velocidad, en menor medida por el avance. Esto queda claro si tenemos en cuenta que el grado de influencia de la velocidad sobre la temperatura de corte es aproximadamente 2 veces superior al del avance.
1. determinar la velocidad de corte según los datos iniciales;
2. determinar el tiempo de procesamiento de acuerdo con los datos iniciales;
Datos iniciales:
Para determinar la velocidad de corte
1. D1 - diámetro del orificio -10 mm;
2. n - 800 rpm;
Para determinar el tiempo de procesamiento
1. n - 800 rpm;
2. id - profundidad de perforación -10 mm;
3. Fr - avance por revolución - 0,15 mm / rev.
4. V – velocidad de corte 25m/min
5. I - el número de agujeros.
6. Vс – velocidad de corte 25,12 m/min
Figura 1. Croquis de la pieza
Solución del problema 5.
1. La velocidad de corte está determinada por la fórmula:
Vc \u003d n * D * n / 1000 \u003d 3.14 * 10 * 800 / 1000 \u003d 25.12 m / min
2. Cálculo del tiempo de procesamiento al perforar:
Determine la frecuencia de rotación:
n \u003d Vc * 1000 / D1 * n \u003d 50 * 1000 / 10 * 3.14 \u003d 1592 rpm
Tc \u003d D1 * 1 / n * Fr \u003d 10 * 1 / 1592.12 * 0.15 \u003d 0.04
0,04 * 60 = 2,5 segundos
EVALUACIÓN DEL DESEMPEÑO
tarea orientada a la competencia 5.
"Cálculo de la velocidad de corte y tiempo de mecanizado al taladrar un agujero"
especialidad
Tecnología de ingeniería
Número de empleo | Contenido de trabajo | Criterios de evaluación | La puntuación máxima por completar la tarea. |
Determinar la velocidad de corte según los datos Determinar el tiempo de mecanizado según los datos Alineación correcta de la pieza en el tornillo de banco Ejecución correcta de la operación de taladrado Control de calidad y tiempo según cálculos | - la capacidad de elegir la fórmula correcta - la capacidad de elegir la fórmula correcta Según aquellos. proceso de acuerdo con las normas TB De acuerdo con el proceso técnico de acuerdo con las normas TB Geometría correcta de la colocación del orificio en la pieza | ||
Máximo de puntos - 25 puntos Marcar "2" - menos de 8 puntos Marcar "3" - 8 - 13 puntos Marcar "4" - 14 - 19 puntos Marcar "5" - 20 - 25 puntos completando la tarea: 1. error aritmético en el cálculo - 3 puntos 2. Error en la realización de aquellos. proceso - 2 puntos |
Tabla de control de calidad del trabajo
Tecnología de ingeniería
PM.03. Participación en la implementación procesos tecnológicos fabricación de piezas de máquinas e implementación de control tecnológico.
MDK.03.01. Implementación de procesos tecnológicos para la fabricación de piezas
Tarea 6.
Selección de parámetros y fórmulas para calcular el diámetro de un orificio para una rosca.
2. realizar la operación de perforación según el cálculo
Datos iniciales:
1. Croquis de una pieza de acero;
2. Materiales St10
Figura 1. Croquis de una forja de acero
Solución del problema 6.
Cálculo del diámetro del agujero para rosca métrica M10
El paso de rosca se toma de la tabla.
Para rosca métrica si no se especifica el paso (por defecto según GOST)
entonces paso = 1,5 mm
de la tabla anterior tomamos el valor correspondiente al paso 1.5, será igual a -1.55
restar este valor de 10
obtenemos el diámetro nominal del agujero con una tolerancia de 8,45+0,17
M10 x1.5 \u003d 10-1.55 \u003d 8.45 + 0.17 mm
EVALUACIÓN DEL DESEMPEÑO
tarea orientada a la competencia 6.
"Selección de parámetros y fórmulas para calcular el diámetro de un orificio para una rosca"
controlar el nivel de formación de competencias profesionales en el marco del desarrollo de módulos profesionales
En el proceso de formación de un orificio, el taladro realiza simultáneamente movimientos de rotación y traslación, mientras que los bordes cortantes del taladro cortan capas delgadas de material, formando astillas. Cuanto más rápido gira la broca y mayor es la distancia que supera en una revolución en la dirección del eje del orificio que se está mecanizando, más rápido se produce el corte.
La velocidad de corte depende según la frecuencia de rotación del taladro y su diámetro, el movimiento del taladro a lo largo del eje de la pieza de trabajo en una revolución afecta el grosor del material eliminado (virutas). El taladro, en comparación con otras herramientas de corte, funciona en condiciones bastante difíciles, ya que al perforar es difícil eliminar las virutas y suministrar refrigerante.
Los elementos principales del corte durante la perforación son la velocidad y la profundidad de corte, el avance, el grosor y el ancho de la viruta (Fig. 3.77).
Velocidad de corte V: el camino recorrido por el punto en el borde de corte del taladro, el más alejado del eje de su rotación. La velocidad de corte está determinada por la fórmula V = ndnl1000 (donde V es la velocidad de corte, m/min; d es el diámetro de la broca, mm; n es la velocidad del husillo, rpm; n es un número constante igual a 3,14; el número 1 OOO se ingresa en la fórmula para convertir el diámetro de perforación a metros). El valor de la velocidad de corte depende del material de la pieza de trabajo, el material de la herramienta y la forma de su afilado, avance, profundidad de corte y la presencia de enfriamiento durante el procesamiento del orificio.
El avance 3 se mide en milímetros por revolución de la broca (mm/rev). La cantidad de avance durante el taladrado se selecciona según los requisitos de rugosidad de la superficie mecanizada y la precisión del mecanizado, el material que se mecaniza y el material que se taladra.
Profundidad de corte t mide en milímetros y representa la distancia desde la superficie mecanizada hasta el eje del taladro, es decir al perforar, la profundidad de corte es la mitad del diámetro de la broca, y al escariar, es la mitad de la diferencia entre el diámetro del orificio pretaladrado y el diámetro de la broca.
Espesor de corte (virutas) se mide en la dirección perpendicular al borde de corte de la broca, y es igual a la mitad de la cantidad de movimiento de la broca en relación con el eje del agujero que se está maquinando en una de sus revoluciones, es decir la mitad de la velocidad de avance. Dado que una capa de material se elimina en una revolución del taladro mediante dos dientes de corte, cada uno de estos dientes elimina una capa de material cuyo espesor es igual a la mitad de la velocidad de avance del taladro por revolución.
Ancho de corte medida a lo largo del filo e igual a su longitud. Al escariar, el ancho de corte es igual a la longitud del borde de corte involucrado en el corte. El ancho de corte se mide en milímetros.
Las condiciones de corte se establecen para proporcionar el mejor rendimiento. En este caso, es necesario tener en cuenta las propiedades físicas y mecánicas del material de la pieza de trabajo que se está procesando, las propiedades del material de la herramienta y los requisitos para la calidad de la superficie mecanizada especificada por el dibujo o las especificaciones técnicas. para fabricación.
Se realiza el cálculo teórico de los elementos del modo de corte. en la secuencia de abajo.
1. Según tablas de referencia especiales, la velocidad de avance se selecciona según el xapat de mecanizado, los requisitos para la calidad de la superficie mecanizada, el material del taladro y otros datos tecnológicos.
2. La velocidad de la herramienta se calcula teniendo en cuenta las capacidades tecnológicas, las propiedades de corte del material de la herramienta y las propiedades físicas y mecánicas de la pieza de trabajo que se procesa.
3. Determine la velocidad del husillo calculada de acuerdo con la velocidad de corte encontrada. El valor obtenido se compara con los datos de pasaporte de la máquina y se toma igual al valor más bajo más cercano de esta frecuencia.
4. Determine la velocidad de corte real con la que se realizará el procesamiento.
En la práctica, para determinar las condiciones de corte, se utilizan datos preparados de mapas tecnológicos y tablas de referencia.
Los modos de corte para avellanado y escariado, así como los criterios para su selección, prácticamente no difieren de la elección de estos parámetros para taladrar.
Concesiones de agujeros
Una tolerancia es una capa de material que se eliminará durante el procesamiento. El tamaño de esta Capa depende de los requisitos de la superficie mecanizada y del tipo de tratamiento.
Al taladrar, el margen de mecanizado es la mitad del diámetro de la broca. Al escariar, la tolerancia se determina según los requisitos para la superficie mecanizada y la necesidad de su procesamiento posterior (escariado, escariado). El margen de fresado, según sea preliminar (antes del despliegue) o definitivo, es de 0,5 a 1,2 mm. El tamaño de la tolerancia también depende del diámetro del orificio que se está maquinando. La tolerancia de escariado depende del diámetro del agujero que se está mecanizando y de los requisitos de calidad de la superficie mecanizada y oscila entre 0,05 y 0,3 mm. Los defectos típicos en el procesamiento de agujeros, las causas de su aparición y los métodos de prevención se dan en la Tabla. 3.2.