1.1. Набуття навичок призначення режимів різання, вибору ріжучого інструменту та розрахунку основного часу.
2.1. Записати дані умов обробки для свого варіанта;
2.2. Вибір різального інструменту, виконання розрахунку режимів різання;
2.3. Оформлення роботи
3. Перелік приладдя
3.1. Папір письмовий, формат А4 - 4 л.;
3.2. Калькулятор, що виконує функції yх.
3.3 Прикладна програма КОМПАС 3D V11
4. Загальні відомості
4.1. Свердління є одним із найпоширеніших методів отримання отвору. Ріжучим інструментом тут служить свердло, яке дає можливість одержувати отвори в суцільному матеріалі та збільшувати діаметр раніше.
просвердленого отвору. Головний рух при свердлінні – обертальний, рух подачі – поступальний.
За формою та конструкції розрізняють свердла спіральні, з прямими канавками, перові, для глибокого свердління, кільцеві, центрувальні, з канавками для підведення мастильно-охолоджувальної рідини, з багатогранними пластинами. Свердла виконують з циліндричним, конічним хвостовиком.
Основні розміри та кути леза свердла стандартизовані. Ріжуча частина свердла виготовляється із сталі Р18, Р6М5 та з твердих сплавів.
Хвостовики свердел з конічним хвостовиком мають конус Морзе, виконаний згідно з ГОСТ 25557-82.
5. Порядок виконання роботи
5.1. Записати дані свого варіанта (див. таблицю 14);
5.2. Вибрати свердло та встановити значення його геометричних елементів.
5.3. Встановити глибину різання t=D /2 (мм) при свердлінні в суцільному металі
t = , мм при розсвердленні раніше виконаного отвору
5.4. Призначити подачу. При свердлінні отворів без обмежуючих факторів вибираємо максимально допустиму за міцністю свердла. При розсвердленні отворів подача, рекомендована для свердління, може бути збільшена до 2 разів.
Sо, мм/об - при свердлінні сталі, чавуну, мідних та алюмінієвих сплавів
5.5. Призначаємо швидкість головного руху різання
V = , м/хв – при свердлінні
V = , м/хв – при розсвердленні
Км - коефіцієнт на оброблюваний матеріал
-Поправочний коефіцієнт, що враховує глибину отвору, що обробляється.
5.6. Визначити частоту обертання шпинделя
про/хв
D -діаметр отвору, мм.
Коригуємо частоту обертання шпинделя за паспортними даними верстата. Приймаємо менше найближче значення n dпро/хв.
5.7. Визначаємо дійсну швидкість різання , м/хв
5.8. Визначаємо крутний момент
Мкр = 10 см Kp – при розсвердленні
Значення коефіцієнтів та показників ступеня
5.9. Визначаємо потужність, що витрачається на різання
(К.п.д.)
5.10. Визначаємо основний час
5.11. Висновок- Потужність верстата дозволяє виконати обробку при даному режимі різання. Якщо N рез.об > N шп — необхідно визначити завантаження верстата за потужністю
Для короткочасного різання (тривалістю до 1 хв) допускається навантаження електродвигуна верстата на 25 % його номінальної потужності. У разі більшого навантаження необхідно зменшити швидкість або взяти потужніший верстат.
6. Вимоги до оформлення розрахунку
6.1. Виконане завдання оформляється на стандартних аркушах формату А4. Перший лист титульний (див. додаток 1)
Приклад виконання завдання
Варіант №31
Завдання: На вертикально-свердлильному верстаті 2Н 135 виробляють свердління отвору діаметром D та глибиною l. Необхідно: вибрати різальний інструмент, призначити режим різання, визначити основний час (див. слайд 1 додаток 3.1).
Таблиця 13
Вибір різального інструменту(Див. слайд 2 додаток 3.2)
Свердло Ø18 з конічним хвостовиком із сталі Р18. ГОСТ 10903-64
Геометричні елементи: форма заточування - подвійна з підточуванням поперечної кромки.
Кути свердла 2 φ = 118 °, 2 φ1 = 70 0 .
ﮯγ = 25°
Призначення елементів різання(Див. слайд 3 додаток 3.3)
1. Визначаємо глибину різання
t = 18/2 = 9мм
2. Призначаємо подачу
S = (0,33 - 0,38) мм / об
До 1 = 0,9 (глибина свердління до 5D)
Тоді Sо = (0,33 - 0,38) * 0,9 = (0,3 - 0,34) мм / об
Коригуємо за паспортом верстата
Sо = 0,28 мм/про
3. Визначаємо швидкість різання
V = , м/хв
Сv = 9.8 q = 0.4 y = 0.5 m = 0.2
— загальний коефіцієнт поправки на швидкість різання
км = Кr Kr = 0.95 n = 1 км = 0,9
-поправочний коефіцієнт, що враховує вплив інструментального матеріалу
-Поправочний коефіцієнт, що враховує глибину отвору, що обробляється.
0,9 1 0,85 = 0,765
V = 0,765 = 21м/хв
4. Число оборотів шпинделя
n д = 355 об/хв (за паспортом верстата)
5. Визначаємо дійсну швидкість різання
6. Визначаємо крутний момент
Мкр = 10 см Kp – при свердлінні
см = 0,0345 q = 2 y = 0.8
Кр = Кмр = 0,9
Мкр = 0,0345 0,9 = 3,62 Н м
7. Визначаємо потужність, витрачену на різання
N = = 0,13 кВт
Перевіряємо, чи достатня потужність приводу верстата
(К.п.д.)
Nшп = 4,5 0,8 = 3,6 кВт
8. Визначаємо основний час
y = 7 мм.
(Див. слайд 4 додаток 3.4)
Ескіз обробки (див. слайд 5 додаток 3.5)
На вертикально-свердлильному верстаті 2Н135 проводять свердління отвору діаметром D і глибиною l.
Необхідно: вибрати різальний інструмент, призначити елементи режиму різання; визначити основний час.
Таблиця 14
№ варіанта | Матеріал заготівлі | D | l | Отвір | Обробка |
мм | |||||
Сталь 10 σв = 35 кгс/мм 2 | 15Н12 | Глухе | З охолодженням | ||
Сталь 40 σв= 45 кгс/мм 2 | 22Н14 | Наскрізне | З охолодженням | ||
Сірий чавун 200НВ | 16Н14 | Наскрізне | Без охолодження | ||
Сталь 40 Х σв= 55 кгс/мм 2 | 18Н13 | Наскрізне | З охолодженням | ||
Сталь 20 Х 170 НВ | 20Н14 | Наскрізне | З охолодженням | ||
Сірий чавун 210 НВ | 10Н14 | Глухе | Без охолодження | ||
Сталь 12Х3 σв= 45 кгс/мм 2 | 19,2Н14 | Глухе | З охолодженням | ||
Сталь 35 Х σв=48 кгс/мм 2 | 24Н14 | Глухе | З охолодженням | ||
Сірий чавун 170 НВ | 18,25 | Наскрізне | Без охолодження | ||
Сталь 20 σв=38 кгс/мм 2 | 15Н12 | Глухе | З охолодженням | ||
Сталь 45 σв=44 кгс/мм 2 | 26Н12 | Глухе | З охолодженням | ||
Ковкий чавун 180 НВ | 24Н12 | Глухе | Без охолодження | ||
Сталь 5 Х НМ σв=70 кгс/мм 2 | 18Н12 | Наскрізне | З охолодженням | ||
Сталь У7А σв=58 кгс/мм 2 | 20Н12 | Наскрізне | З охолодженням | ||
Сталь 65Г σв = 50 кгс/мм 2 | 25Н12 | Наскрізне | З охолодженням | ||
Сірий чавун 210НВ | 28Н12 | Глухе | Без охолодження | ||
Сталь 40 Х 13 σв = 65 кгс/мм 2 | 24Н12 | Глухе | З охолодженням | ||
Сталь 9 х С σв= 60 кгс/мм 2 | 20Н12 | Наскрізне | З охолодженням | ||
Ковкий чавун 220 НВ | 26Н12 | Наскрізне | Без охолодження | ||
Сталь 40 Х З 225 НВ | 8Н12 | Наскрізне | З охолодженням | ||
Сталь 30Л σв=50 кгс/мм | 6Н12 | Наскрізне | З охолодженням | ||
Сталь А20 σв=30 кгс/мм 2 | 12Н12 | Наскрізне | З охолодженням | ||
Сталь 35 σв= 50 кгс/мм 2 | 14Н12 | Глухе | З охолодженням | ||
Сірий чавун 175 НВ | 16Н12 | Глухе | Без охолодження | ||
Сталь 40 Г σв= 55 кгс/мм 2 | 16,8Н12 | Глухе | З охолодженням | ||
26 | Сталь Х12М δв= 60 кгс/мм 2 | 17,2Н12 | Наскрізне | З охолодженням | |
Сталь ХВГ σв = 55 кгс/мм | 18,25Н12 | Наскрізне | З охолодженням | ||
Сірий чавун 170 НВ | 24Н12 | Наскрізне | Без охолодження | ||
Латунь ЛМцЖ 52-4-1 100 НВ | ЗОН12 | Наскрізне | Без охолодження | ||
Бронза БРАЖН 11-6-6 200 НВ | 24Н12 | Наскрізне | Без охолодження |
Обробка отворів проводиться різними різальними інструментами в залежності від виду заготовки, необхідної точності та потрібної чистоти поверхні.
Розрізняють заготовки з отворами, підготовленими при виливку, кування або штампування, та заготовки без попередньо підготовлених отворів.
Обробку отворів у заготовках, які мають попередньо підготовлених отворів, завжди починають зі свердління.
1. Свердла
Свердління неглибоких отворів виробляють перовими та спіральними свердлами.
Перове свердло. Перовий свердло показано на рис. 159. Ріжуча частина свердла представляє плоску лопатку 3, що переходить у стрижень 4. Дві ріжучі кромки 1 і 2 свердла нахилені один до одного зазвичай під кутом 116-118°, але цей кут може бути рівним від 90 до 140°, залежно від твердості оброблюваного матеріалу: чим матеріал твердіше, тим більший кут.
Перові свердла малопродуктивні, крім того, при свердлінні їх відводить убік від осі отвору. Незважаючи на це, їх іноді застосовують для невідповідальних робіт, що пояснюється простотою конструкції таких свердл та їх невисокою вартістю.
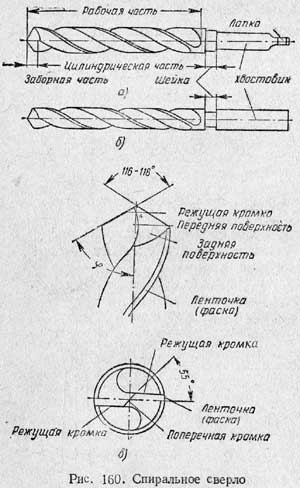
Спіральні свердла. В даний час свердління виробляють головним чином спіральними свердлами. На рис. 160 показано таке свердло. Воно складається з робочої частиниі хвостовика(конічного по рис. 160, або циліндричного по рис. 160, б) для кріплення свердла або в конічному отворі пінолі задньої бабки, або в патроні.
Конічний хвостовик має лапку, яка є упором при вибиванні свердла (рис. 160, а).
Робоча частина спірального свердла є циліндром з двома спіральними (вірніше - гвинтовими) канавками, службовцями для утворення ріжучих кромок свердла і виведення стружки назовні. Передня частина свердла (рис. 160 в) заточена по двох конічних поверхнях і має передню поверхню, задню поверхню, дві ріжучі кромки, з'єднані перемичкою(Поперечною кромкою). Дві вузькі стрічки(фаски), що йдуть вздовж гвинтових канавок свердла, служать для правильного напрямку та центрування свердла.
Кут при вершині свердла 2? зазвичай дорівнює 116 - 118 °. Для свердління твердих матеріалів цей кут збільшують до 140°, а свердління м'яких матеріалів його зменшують до 90°.
Свердла виготовляють з легованої сталі 9ХС, швидкорізальної сталі Р9 і Р18, а також з легованої сталі з пластинами припаяними твердого сплаву.
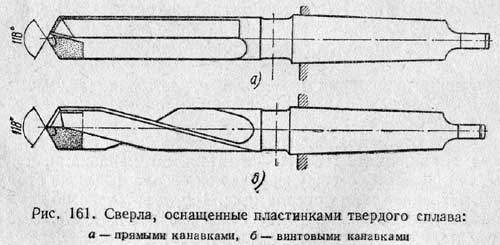
Свердла, оснащені пластинками твердого сплаву, показано на рис. 161. Свердла з прямими канавками (рис. 161, а) простіше у виготовленні, але вихід стружки з отвору у них утруднений; їх зазвичай застосовують при свердлінні чавуну та інших крихких металів, коли глибина отвору не перевищує двох-трьох діаметрів. Свердла з гвинтовими канавками (рис. 161 б) легше виводять стружку з отвору, тому їх рекомендується застосовувати при свердлінні в'язких матеріалів.
2. Заточування спіральних свердлів
Заточування спіральних свердлів роблять на спеціальних верстатах. Однак токареві іноді доводиться заточувати свердла вручну на звичайному точилі.
При заточуванні свердлів потрібно дотримуватися таких умов:
1. Ріжучі кромки свердла мають бути симетричні, Т. е. розташовані під певними і рівними кутами до осі свердла і мати однакову довжину.
2. Поперечна кромка (перемичка) повинна бути розташована під кутом 55° до ріжучих кромок (рис. 160 ст).
Заточений таким чином свердло працюватиме добре.
На рис. 162 показані отвори, одержувані при свердлінні правильно та неправильно заточеними свердлами. При однаковій довжині ріжучих кромок (рис. 162 а) діаметр просвердленого отвору дорівнює діаметру свердла. Якщо ж одна кромка довша за іншу (рис. 162, б), то діаметр отвору виходить більше діаметра свердла. Це може призвести до шлюбу та швидко вивести свердло з ладу через нерівномірне навантаження ріжучих кромок.
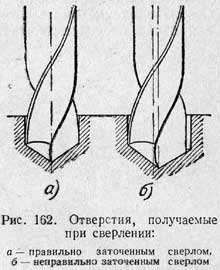
Правильність заточування свердла перевіряється спеціальним комбінованим шаблоном з трьома вирізами (рис. 163 а); одним з вирізів перевіряють кут при вершині свердла та довжину ріжучих кромок (рис. 163 б), другим вирізом - кут загострення ріжучої кромки на зовнішньому діаметрі свердла (рис. 163, в), третім - кут між перемичкою і ріжучою кромкою (мал. 163, г).
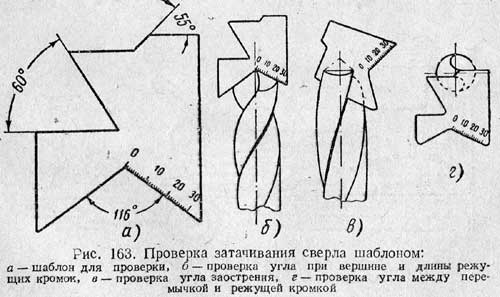
3. Закріплення свердл
Спосіб закріплення свердла залежить від форми хвостовика. Свердла з циліндричним хвостовикомзакріплюють у пінолі задньої бабки за допомогою спеціальних патронів (рис. 164); свердла з конічним хвостовикомзакріплюють безпосередньо в конічному отворі пінолі задньої бабки (рис. 165). Конічні хвостовики інструментів, а також конічні отвори в шпинделях і пінолях токарних верстатів виготовляються за системою Морзе. Конуси Морзе мають номери 0, 1, 2, 3, 4, 5, 6; кожному номеру відповідає певний розмір. Якщо конус свердла менше конічного отвору пінолі задньої бабки, то на хвостовик 1 свердла надягають перехідну втулку 2 (рис. 166) і потім втулку разом зі свердлом вставляють в отвір пінолі задньої бабки верстата.
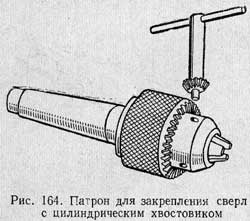
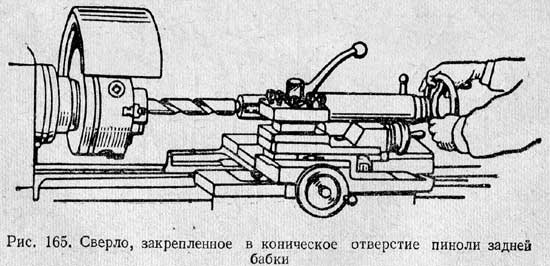
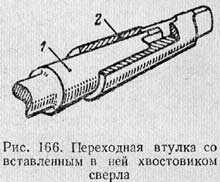
Перед тим як вставити свердло в пінолі задньої бабки, необхідно ретельно очистити від бруду хвостовик свердла, а також отвір пінолі.
Щоб видалити свердло з пінолі задньої бабки, слід повертати маховичок доти, доки піноль не буде затягнута в корпус задньої бабки до останнього положення. У цьому положенні гвинт упирається в торець хвостовика і виштовхне його.
4. Прийоми свердління
Підготовка до свердління. При свердлінні отвору довжиною більше двох діаметрів свердла рекомендується спочатку отвір жорстко закріпленим у пінолі коротким Тоді наступне свердло краще прямуватиме і його менше буде вести убік.
Подача свердла. Подачу свердла здійснюють обертанням маховичка задньої бабки (рис. 165).
При свердлінні глибокого отвору спіральним свердломпотрібно іноді виводити свердло з отвору на ходу верстата і видаляти зі стружку; цим запобігає поломці свердла. Необхідно також стежити за тим, щоб при свердлінні нормальними свердлами глибина отвору була більше довжини спіральної канавки свердла, оскільки інакше стружка зможе виходити з канавок і свердло зламається.
Свердління глухих отворів. Для свердління отворів заданої довжини зручно користуватися ризиками з на пінолі задньої бабки (див. рис. 165). Обертанням ма-висувають свердло, поки воно не заглибиться в матеріал де-всей забірною частиною, і помічають при цьому відповідну ризику на пінолі. Потім, обертаючи маховичок задньої бабки, переміщують пінолю доти, доки вона не вийде з корпусу на потрібну кількість поділів.
Коли на пінолі немає поділів, можна застосувати такий спосіб. Відзначають на свердлі крейдою необхідну довжину отвору і переміщують пінолю, поки свердло не заглибиться в мітки.
Іноді при свердлінні чується характерний металевий вереск. Це є ознакою перекосу отвору чи затуплення свердла. У таких випадках треба негайно припинити подачу, зупинити верстат, з'ясувати та усунути причину вереску.
Перш ніж зупинити верстат під час свердління, вивести свердло з отвору. Зупиняти верстат у той час, коли свердло знаходиться в отворі, не можна, це може призвести до заїдання свердла та його поломки.
5. Режими різання при свердлінні та розсвердлюванні
Швидкість різання при свердліннівуглецевої сталі середньої твердості, сірого чавуну та бронзи свердлами зі швидкорізальної сталі можна приймати рівною 20-40 м/хв.
Подача свердла на токарному верстаті проводиться зазвичай вручну, повільним переміщенням пінолі задньої бабки, як показано на рис. 165. Занадто велика і нерівномірна подача може призвести до поломки свердла, особливо при використанні свердла малих діаметрів.
Іноді при свердленні застосовується і механічна подача (див. рис. 167). В цьому випадку свердло зміцнюється за допомогою спеціальних прокладок або втулки в держачі. При свердлінні з механічною подачею величину подачі приймають рівною: при свердлах діаметром від 6 до 30 мм для вуглецевої сталі середньої твердості від 0,1 до 0,35 мм1об; для чавуну – від 0,15 до 0,40 мм/об.
При рассверливании поперечна кромка свердла не бере участі у роботі. Завдяки цьому значно зменшується зусилля подачі, зменшується і виведення свердла; це дозволяє збільшувати величину подачі приблизно в 1? рази в порівнянні з подачею свердла того ж діаметра при свердлінні в суцільному матеріалі.
Швидкість різання під час розсвердлюванняможна брати таку ж, як і при свердлінні.
Свердління та розсвердлювання сталі та алюмінію рекомендується вести з охолодженням емульсією у кількості не менше 6 л/хв; чавун, латунь та бронзу свердлять і розсвердлюють без охолодження. Необхідно, однак, відзначити, що через горизонтальне розташування отворів, що обробляються, охолодна рідина насилу подається до місця утворення стружки. Тому для глибокого свердління у важко оброблюваних матеріалах застосовують свердла з внутрішніми каналами, якими подають охолоджувальну рідину під великим тиском до ріжучих кромок.
6. Високопродуктивні методи роботи при свердлінні та розсвердлюванні
Заміна ручної подачі механічної. Новатори виробництва з метою механізації подачі свердла застосовують прості та дешеві пристосування, що полегшують працю та зберігають час. Одне з таких пристроїв показано на рис. 167.
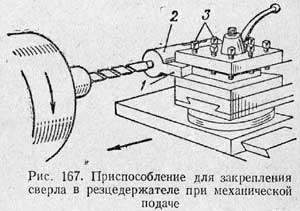
Пристрій є сталевою державкою 2 з плиткою 1, що закріплюється за допомогою болтів 3 в резцедержателе. У державці є конічний отвір для закріплення хвостовика свердла та отвір для вибивання свердла. Нижня площина плитки 1 простругана або профрезерована так, що при закріпленні її в різцетримачі свердло точно (без прокладок) встановлюється на висоті центрів. Щоб встановити свердло по осі отвору в горизонтальній площині, на нижніх санках супорта відзначається ризик. Такий пристрій дуже ефективний при виготовленні великої кількостідеталей з отворами, тому що в цьому випадку свердління проводиться з механічною подачею свердла від супорта; використання його зменшує час обробки і полегшує працю токаря.
Для механізації подачі свердла при свердлінні отворів великого діаметрув умовах дрібносерійного та одиничного виробництва токарем-новатором т. Бучневим виготовлено пристрій (рис. 168 а), що дає можливість пересувати задню бабку з витратою невеликого зусилля. Цей пристрій полягає у наступному. До плити задньої бабки кріплять болтами кутовий кронштейн 5, в якому поміщаються валики 1 і 2. На валику 1 сидить провідне зубчасте колесо 7 і рукоятка 6. На валику 2 знаходиться зубчасте колесо 3 і 4 колесо, що зчепляється з рейкою станини. Обертання рукоятки 6 через колеса 7 і 3 передається колесу 4, яке котиться по рейці верстата і пересуває задню бабку по станині.
На токарно-гвинторізному верстаті 1К62 заводу «Червоний пролетар» передбачено заміну ручної подачі свердла (зенкера, розгортки) механічною. Для цього в супорті є спеціальний замок (рис. 168 б), що входить в приплив задньої бабки. За допомогою такого легкого пристрою можна з'єднати каретку супорта з плитою задньої бабки і, звільнивши плиту задньої бабки від станини, включити найвигіднішу механічну подачу супорта.
Продуктивність праці у своїй значно підвищується. Крім зазначеної переваги, такий спосіб подачі дозволяє робити свердління (зенкерування, розгортання) отворів на необхідну глибину, ведучи відлік по лімбу поздовжньої подачі або користуючись поздовжнім упором (довгообмежувачем).
Використання свердл особливого заточування. Для підвищення продуктивності праці новатори виробництва застосовують підточування перемички, використовують подвійне заточування свердел і безперемичне свердла.
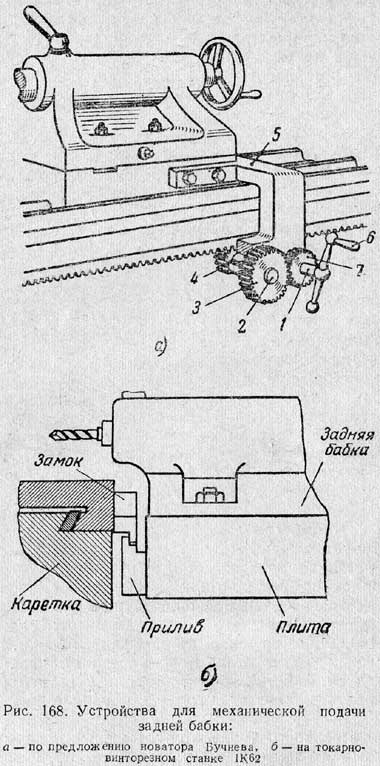
Свердло з подвійним заточуваннямпоказано на рис. 169 а. Забірна частина має ламані ріжучі кромки: спочатку короткі під кутом 70-75°, а до вершини подовжені - під кутом 116-118°. Такі свердла зношуються менше нормальних і відрізняються підвищеною стійкістю - у 2 - 3 рази більшою при свердлінні сталі та у 3 - 5 разів більшою при свердлінні чавуну.
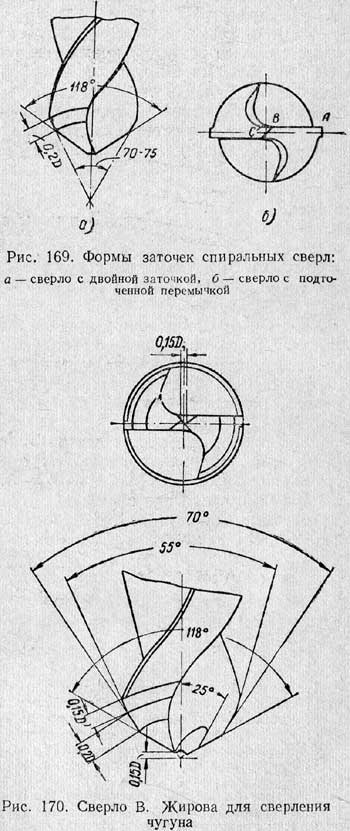
Для зменшення зусилля подачі при свердлінні корисної виявляється підточування перемички на ділянці ПС (рис. 169, б). При такій підточці не лише зменшується поперечна кромка, а й збільшується передній кут, що полегшує умови різання.
На рис. 170 показано високопродуктивне свердло з швидкорізальної сталі швидкісника - свердлувальника Середньоволзького верстатобудівного заводу В. Жирова. Свердло призначене для свердління чавуну.
Свердло Жирова на відміну свердла, показаного на рис. 169 а, виготовляється з потрійним конусом у вершини, з підточеною передньою поверхнею і прорізаною перемичкою. Наявність виїмки замість перемички значно полегшує врізання свердла в метал, що обробляється, завдяки чому в 3-4 рази знижується осьове зусилля при свердлінні чавуну. Це дозволяє збільшити подачу свердла та скоротити машинний час принаймні вдвічі.
Для підвищення стійкості забірна частина свердла Жирова має три ламані ріжучі кромки, спочатку короткі, що утворюють кут 55 °, потім довші - з кутом 70 ° і, нарешті, найдовші - з кутом у вершини 118 °.
Наявність коротких ріжучих кромок з кутом 55 ° сприяє значному підвищенню стійкості свердла (при роботі з підвищеними подачами) порівняно з звичайною свердлами конструкції.
7. Шлюб при свердлінні та заходи його попередження
Основний вид шлюбу при свердлінні - відведення свердла від необхідного напрямку, найчастіше спостерігається при свердлінні довгих отворів.
Виведення свердла відбувається: при свердлінні заготовок, у яких торцеві поверхні не перпендикулярні до осі; під час роботи довгими свердлами; при роботі неправильно заточеними свердлами, у яких одна ріжуча кромка довша за іншу; при свердлінні металу, який має раковини або містить тверді включення.
Виведення свердла при роботі довгими свердлами можна зменшити попереднім надсвердлюванням отвору коротким свердлом того ж діаметра.
Якщо на шляху свердла в матеріалі деталі зустрічаються раковини або тверді включення, то в цьому випадку запобігти виведенню свердла майже неможливо. Його можна лише зменшити шляхом зменшення подачі, що водночас з'явиться засобом попередження можливої поломки свердла.
Контрольні питання 1. Які типи свердлів застосовуються під час свердління на токарних верстатах?
2. Назвіть елементи спірального свердла.
3. Розкажіть про правила заточування свердлів.
4. Як позначиться на розмірах отвору неправильне заточення свердла?
5. Якими способами закріплюються свердла у верстат?
6. Розкажіть про прийоми свердління наскрізних отворів, глухих отворів:
7. Яке охолодження застосовують під час свердління?
8. Розкажіть про передові способи свердління.
9. Як попередити відведення свердла?
Сили різання, момент та потужність при свердлінні
У процесі різання свердло відчуває опір з боку матеріалу, що обробляється. На кожну точку ріжучої кромки діють сили опору. Замінимо їх рівнодіючою силою, прикладеною до точки А на відстані приблизно рівному D /4 від осі свердла. Останню можна розкласти на три складові сили Р x , Р у і Р z (Мал.72.)
Мал. 72. Сили, що діють на свердло
Сила опору Р х спрямована вздовж осі свердла. У цьому напрямі діє сила Р п на поперечну кромку, сила тертя Р т стрічки об поверхню отвору, сили опору, що діють на свердло вздовж її осі, на вісь X замінимо рівнодіючою силою Р 0 яка називається осьовою силою або силою подачі. Вона долається механізмом подачі верстата. Останній повинен передати на шпиндель верстата осьову силу Р" 0 , здатну подолати силу Р 0 . Максимальна осьова сила, що допускається механізмом подачі верстата, наводиться у паспорті.
Формули для підрахунку осьової сили та моменту при свердлінні:
Визначення сили Р 0 та моменту М кр проводиться за емпіричними формулами, отриманими експериментальним шляхом. Для свердл з інструментальних сталей при обробці сталевих та чавунних деталей вони мають такий вигляд:
; , кГс·мм - при свердлінні;
; , кГс·ммпри розсвердлювання.
де: З р і З м - Коефіцієнти, що залежать від оброблюваного металу, форми заточування свердла та умов різання;
z p, x p , y p , z M , x M і y M – ступеня впливу діаметра свердла D , глибини різання t , подачі s на осьову силу P 0 і крутний момент при свердлінні М ;
K pі K M - Поправочні коефіцієнти на змінені умови свердління;
Радіальні сили Р у , різноспрямовані, врівноважуються (S Р у = 0). Сила Р z створює момент опору різанню М на головних ріжучих кромках, а сила Рт', що стосується стрічки, - момент тертя на ній (їм зазвичай нехтують).
Відносний вплив елементів свердла на силу різання та момент кручення при свердлінні наведено у таблиці 16.
Таблиця 16. Вплив елементів свердла на осьову силу P 0 ікрутний момент М
Момент опору різанню M рез долається механізмом головного руху, тобто крутним моментом на шпинделі верстата М кр . На кожному щаблі шпинделя верстата потужність N шп постійна, момент М крзмінний. Він залежить від частоти обертання (числа оборотів) п на даному ступені і визначається:
М кр= 716200 · 1,36 · () кГс мм; N шп = N дв · h , КВт,
М кр= 974000 · () кГс мм.
Знаючи момент опору М , можна визначити ефективну потужність N е витрачається на різання при свердлінні,
Потужність на подачу свердла становить близько 1% від потужності та в розрахунках не враховується. За потужністю визначають потужність, яку повинен мати електродвигун верстата для забезпечення заданого процесу різання:
, кВт
Верстат придатний для заданих умов свердління, якщо N шп > N e .
6.4. Вплив різних факторів на осьову силу та момент при свердлінні.На осьову силу Р 0 та момент опору різанню М впливають властивості оброблюваного матеріалу, геометричні параметри свердла, елементи зрізу (діаметр, подача) та ін.
6.4.1. Властивості оброблюваного матеріалу. Чим вище межа міцності σ в та твердість НВ матеріалу, тим більше його опір різання, тим вище значення Р 0 і М . Для свердл із швидкорізальної сталі отримані експериментально такі залежності:
, І - для сталі;
і - для чавуну.
де: З р і З м - Коефіцієнти, що залежать від умов різання.
6.4.2. Геометричні параметри свердла. Зі збільшенням кута w осьова сила Р 0 та момент М зменшуються у зв'язку із збільшенням передніх кутів γ х на головних ріжучих кромках та полегшенням відведення стружки. Кут j , (2j ) впливає на складові сили різання та момент за аналогією з точенням: при зменшенні кута осьова сила Р 0 зменшується, а тангенціальна Р z збільшується, тим самим збільшується та М . Зі зменшенням кута 2 j опір різання у зв'язку із збільшенням γ х зменшується, але одночасно збільшується ширина зрізу та зменшується його товщина. Останнє веде до зростання деформації (тонкі стружки деформуються повніше) і, отже, зростання сили Р x та моменту М . Кут нахилу поперечної кромки d > 90° (див. рис. 72) і це значно збільшує осьову силу Р 0 . Раніше було зазначено, що сила, що діє на поперечну кромку Рп = 0,55Р 0 . Для її зниження зменшують довжину кромки шляхом підточування, збільшують її передній кут, тим самим створюються сприятливіші умови різання поблизу неї. на величину М геометрія поперечної кромки впливає слабко. Подвійне заточування свердла також слабко впливає на Р 0 і М .
Діаметр свердла та подача. Зі збільшенням діаметра свердла D та подачі s збільшуються ширина і товщина шару, що зрізається, отже, зростають сили і момент різання. Експериментально встановлено, що діаметр свердла впливає Р 0 більшою мірою (1), ніж подача (0,8). Для пояснення можна навести аналогію з точенням, де глибина різання t впливає більшою мірою на сили різання, ніж подача (див.), а при свердлінні t = D / 2 мм. Подача впливає приблизно однаковою мірою (0.8) на осьову силу Р 0 і крутний момент М , А діаметр впливає більшою мірою (1,9) на М і в меншій - на Р 0 (1). Це пояснюється тим, що при збільшенні діаметра й зростає сила Р z , що створює момент М , і одночасно збільшується довжина плеча, на якому діє ця сила, що також сприяє збільшенню М (Мал.).
Охолоджуюча рідина. Подача рідини, що охолоджує, в зону різання полегшує відведення стружки, зменшує роботу тертя і уповільнює знос свердла. Вона сприяє зниженню осьової сили Р 0 та моменту М до 25% при обробці сталевих деталей та до 15% - при обробці чавунних.
Знос свердла
Природа та характер зносу свердлів та різців однакові. При обробці в'язких матеріалів (сталів та ін.) швидкорізальними свердлами зношуються передні та задні поверхні свердла (рис. 73.), а у твердосплавних свердл передні поверхні зношуються незначно.
Мал. 73. Характер зносу свердла: А- По задній поверхні; Б- По стрічкі; У– по куточках; Г– по передній поверхні
При обробці крихких матеріалів (чавуну, пластмаси та ін) переважно зношуються задні поверхні та куточки свердла. Передні та задні поверхні свердла більш інтенсивно зношуються на периферії, так як тут швидкість різання найбільша і куточки свердла, будучи ослабленим місцем, сильно нагріваються та руйнуються. Закономірність зносу свердел приблизно така сама, як і різців при точении (Рис. 74).
Мал. 74. Характер протікання зносу свердла від часу роботи
Оцінку зносу рекомендується проводити: при обробці в'язких матеріалів - за довжиною зносу по задніх поверхнях h з для крихких матеріалів - по довжині зносу куточків. h y. Допустима величина зносу -критерій зносу при свердлінні свердлами швидкорізальними:
h З кр= 0,4…1,2 мм, під час обробки стали;
При обробці чавуну швидкорізальними свердлами як критерій зношування приймається зношування по довжині куточків.
h у= 0,4…1,2 мм – обробка свердлом із швидкорізальної сталі;
h у= 0,9...1,4 мм. - Обробка свердлом з твердого сплаву;
Період стійкості Т , хв, залежить від діаметра свердла та оброблюваного матеріалу.
Т= (1,0…1,25)∙D - Обробка стали швидкорізальними свердлами;
T= (1,25…1,5) D - Обробка чавуну швидкорізальними свердлами;
Т= (1,5…2,0) D - Обробка чавуну свердлами з твердого сплаву.
В результаті проведених дослідів при свердлінні стали свердлами, що швидкорізають, отримана наступна залежність:
З отриманих результатів видно, що на зношування свердла більшою мірою впливає швидкість, меншою - подача. Це стає зрозумілим, якщо врахувати, що на температуру різання рівень впливу швидкості приблизно в 2 рази вище, ніж подачі.
1. визначити швидкість різання за вихідними даними;
2. визначити час обробки за вихідними даними;
Вихідні дані:
Для визначення швидкості різання
1. D1 – діаметр отвору –10мм;
2. n - 800об/хв;
Для визначення часу обробки
1. n - 800об/хв;
2. id – глибина свердління -10мм;
3. Fr – подача оборот - 0,15мм/об.
4. V – швидкість різання 25м/хв
5. I – кількість отворів.
6. Vс – швидкість різання 25,12 м/хв
Малюнок 1. Ескіз деталі
Розв'язання завдання 5.
1. Швидкість різання визначаємо за формулою:
Vс = п * D * n / 1000 = 3,14 * 10 * 800 / 1000 = 25,12 м / хв
2. Розрахунок часу обробки при свердлінні:
Визначаємо частоту обертання:
n = Vc * 1000 / D1 * п = 50 * 1000 / 10 * 3,14 = 1592 об / хв
Tс = D1 * 1 / n * Fr = 10 * 1 / 1592,12 * 0,15 = 0,04
0,04*60 = 2,5 сек
ОЦІНКА ВИКОНАННЯ
компетентнісно-орієнтованого завдання 5.
«Розрахунок швидкості різання та час обробки при свердлінні отвору»
спеціальність
Технологія машинобудування
Номер завдання | Зміст завдання | Критерії оцінювання | Максимальний бал за виконання завдання |
Визначити згідно з даними швидкість різання Визначити згідно з даними час обробки Правильна вивірка деталі в лещатах Правильне виконання операції свердління Контроль якості та часу згідно з розрахунками | -уміння правильно вибрати формулу -уміння правильно вибрати формулу Відповідно до тих. процесу з дотриманням правил ТБ Відповідно до тех.процесу з дотриманням правил ТБ Правильність геометрії розміщення отвору на деталі | ||
Максимальна кількість балів - 25 балів Позначка «2» - менше 8 балів Позначка «3» - 8 – 13 балів Позначка «4» - 14– 19 балів Позначка «5» - 20– 25 балів Кількість балів, знижених за помилки, допущені при виконання завдання: 1. арифметична помилка під час розрахунку – 3 бала 2.Помилка під час виконання тех. процесу - 2 бали |
Таблиця перевірки якості виконання завдання
Технологія машинобудування
ПМ.03. Участь у впровадженні технологічних процесіввиготовлення деталей машин та здійснення технологічного контролю.
МДК.03.01. Реалізація технологічних процесів виготовлення деталей
Завдання 6.
Вибір параметрів та формули для розрахунку діаметра отвору під різьблення
2. виконати операцію свердління згідно з розрахунком
Вихідні дані:
1. Ескіз сталевої деталі;
2. Матеріал Ст10
Малюнок 1. Ескіз сталевого поковки
Розв'язання завдання 6.
Розрахунок діаметра отвору під метричне різьблення М10
Крок різьблення беремо з таблиці.
Для метричної різьби якщо крок не вказаний (за умовчанням згідно з ГОСТ)
то крок = 1,5 мм
з таблиці вище беремо значення відповідне кроці 1,5 воно дорівнюватиме -1,55
це значення віднімаємо з 10
отримуємо номінальний діаметр отвору з допуском 8,45+0,17
М10 х1,5 = 10-1,55 = 8,45 +0,17 мм
ОЦІНКА ВИКОНАННЯ
компетентнісно-орієнтованого завдання 6.
«Вибір параметрів та формули для розрахунку діаметра отвору під різьблення»
для контролю рівня сформованості професійних компетенцій у рамках освоєння професійних модулів
У процесі утворення отвору свердло одночасно здійснює обертальний і поступальний рух, при цьому ріжучі кромки свердла зрізають тонкі шари матеріалу, утворюючи стружку. Чим швидше обертається свердло і чим більша відстань за один оберт воно долає в напрямку осі отвору, тим швидше відбувається різання.
Швидкість різання залежитьвід частоти обертання свердла та його діаметра, переміщення свердла вздовж осі заготовки за один оборот впливає на товщину знімається елся матеріалу (стружки). Свердло в порівнянні з іншими різальними інструментами робота, т в досить важких умовах, так як при свердлінні утруднений відведення стружки і підведення змащувально-охолоджуючої рідини.
Основними елементами різання при свердлінні є швидкість та глибина різання, подача, товщина та ширина стружки (рис. 3.77).
Швидкість різання V - шлях, пройдений точкою на ріжучій кромці свердла, найбільш віддаленої від осі обертання. Визначають швидкість різання за формулою V = ndnl1000 (де V-швидкість різання, м/хв; d - діаметр свердла, мм; п - частота обертання шпинделя, об / хв; п - постійне число, що дорівнює 3,14; число 1 ТОВ введено формулу для перекладу діаметра свердла в метри). Величина швидкості різання залежить від матеріалу заготовки, матеріалу інструменту та форми його заточування, подачі, глибини різання та наявності охолодження під час обробки отвору.
Подача 3 вимірюється в міліметрах на один оберт свердла (мм/об). Величина подачі при свердлінні вибирається в залежності від вимог, що пред'являються до шорсткості обробленої поверхні та точності обробки, оброблюваного матеріалу та матеріалу свердлу.
Глибина різання tвимірюється в міліметрах і є відстанню від оброблюваної поверхні до осі свердла, тобто. при свердлінні глибина різання становить половину діаметра свердла, а при розсвердлюванні - половину різниці між діаметром попередньо просвердленого отвору і діаметром свердла.
Товщина зрізу (стружки)вимірюється в напрямку, перпендикулярному ріжучої кромки свердла, і дорівнює половині величини переміщення свердла щодо осі отвору, що обробляється за один його оборот, тобто. половині величини подачі. Оскільки шар матеріалу за один оберт свердла знімається двома ріжучими зубами, то кожен з цих зубів видаляє шар матеріалу, товщина якого дорівнює половині величини подачі свердла на один його оберт.
Ширина зрізувимірюється вздовж ріжучої кромки та дорівнює її довжині. При рассверливании ширина зрізу дорівнює довжині ріжучої кромки, що у різанні. Вимірюється ширина зрізу міліметрах.
Режими різання встановлюються з метою забезпечення максимальної продуктивності. При цьому необхідно враховувати фізико-механічні властивості матеріалу оброблюваної заготовки, властивості матеріалу інструменту та вимоги до якості обробленої поверхні, задані кресленням або технічними умовами виготовлення.
Теоретичний розрахунок елементів режиму різання виконуютьу наведеній нижче послідовності.
1. За спеціальними довідковими таблицями вибирають величину подачі залежно від xapat тера обробки, вимог до якості обробленої поверхні, матеріалу свердла та інших технологічних даних.
2. Розраховують швидкість інструменту з урахуванням технологічних можливостей, ріжучих властивостей матеріалу інструменту та фізико-механічних властивостей оброблюваної заготівлі.
3. Визначають розрахункову частоту обертання шпинделя відповідно до знайденої швидкості різання. Отриману величину порівнюють з паспортними даними верстата та приймають рівною найближчому найменшому значенню цієї частоти.
4. Визначають дійсну швидкість різання, з якою проводитиметься обробка.
Насправді визначення режимів різання використовують готові дані технологічних карт і таблиць довідників.
Режими різання при зенкеруванні та розгортанні, а також критерії їх вибору практично не відрізняються від вибору цих параметрів під час свердління.
Припуски на обробку отворів
Припуск - це шар матеріалу, що підлягає зняттю під час обробки. Величина цього шару залежить від вимог, що пред'являються до обробленої поверхні та виду обробки.
При свердлінні припуск на обробку становить половину діаметра свердла. При розсвердлюванні припуск визначається залежно від вимог до обробленої поверхні та від необхідності її подальшої обробки (зенкерування, розгортання). Припуск на зенкерування, в залежності від того, є попереднім (перед розгортанням) або остаточним, становить від 0,5 до 1,2 мм. Величина припуску залежить також від діаметра отвору, що обробляється. Припуск на розгортання залежить від діаметра отвору, що обробляється, і від вимог, що пред'являються до якості обробленої поверхні і становить від 0,05 до 0,3 мм. Типові дефекти при обробці отворів, причини їх появи та способи попередження наведені у табл. 3.2.